Environment
Fostering a culture of eco-sensitivity
As a responsible entity, we remain committed
to the environment and sustainability, and
our initiatives reflect that devotion.
Decarbonisation

Sustainability is one of the key pillars of our business strategy
that underpins our value creation process. We want to enable a
low-carbon and circular economy, empower our people and communities,
and embed responsible business practices throughout our
organisation.
These ambitions in turn support the UN Sustainable Development Goals
(SDGs).
In line with our strategic focus as a provider of sustainable
solutions, we have adopted SDG 7 (Affordable and Clean Energy), and
SDG 13 (Climate Action) as our priority SDGs. We aim to make a
meaningful commitment in these areas by executing several
environment friendly technologies such as Energy optimisation
projects, Decarbonisation projects.
SEIL continues to explore possibilities of implementing environmentally sustainable technologies in to their processes, for reducing GHG emissions. Following are few of such implemented options
- Increasing of Horticulture and Plantation
- P1&P2-Energy Management system (EMS) Implemented for Auxiliary consumption optimisation
P1&P2 Online GHG monitoring tool implemented for real-time monitoring and optimization from plant end: As applicable, Scope-1 is being reported.
Sea water from the Bay of Bengal is being used to cater to all plant requirements after treatment. Wastewater generated from the process/system is reused for green belt development after treatment.
Being a sea water-based organization, there is no water scarcity risk. The healthiness of the intake system is ensured through periodic inspection.
Flowmeters are installed in the water intake and discharge line to monitor the water consumption and discharge quantity. Discharge water quality is monitored and controlled before discharging into the sea as per stipulated guidelines.
SEIL - Using sea water is the main source for generating DM water for plant operation.
No major risks are confronted.
Sea water is the primary source for generating DM water for plant operation. The sea water intake system's healthiness is ensured by continuous monitoring and periodic maintenance.
Water consumption is monitored on a daily basis. This leads to identification and analysis for further optimization. System-wise benchmarks are identified, and consumption is controlled.
A water monitoring group has been formed to carry out system-wise water audits periodically for conserving water.

Environmental Stewardship:
SEIL is dedicated to cultivating a thriving green ecosystem by establishing a dense greenbelt around our operational areas. To date, we have planted more than 1.1 million saplings spanning 60 diverse species on about 900 acres. Our plant selection process prioritises eco-suitability and sustainability, ensuring a harmonious balance with the local environment.
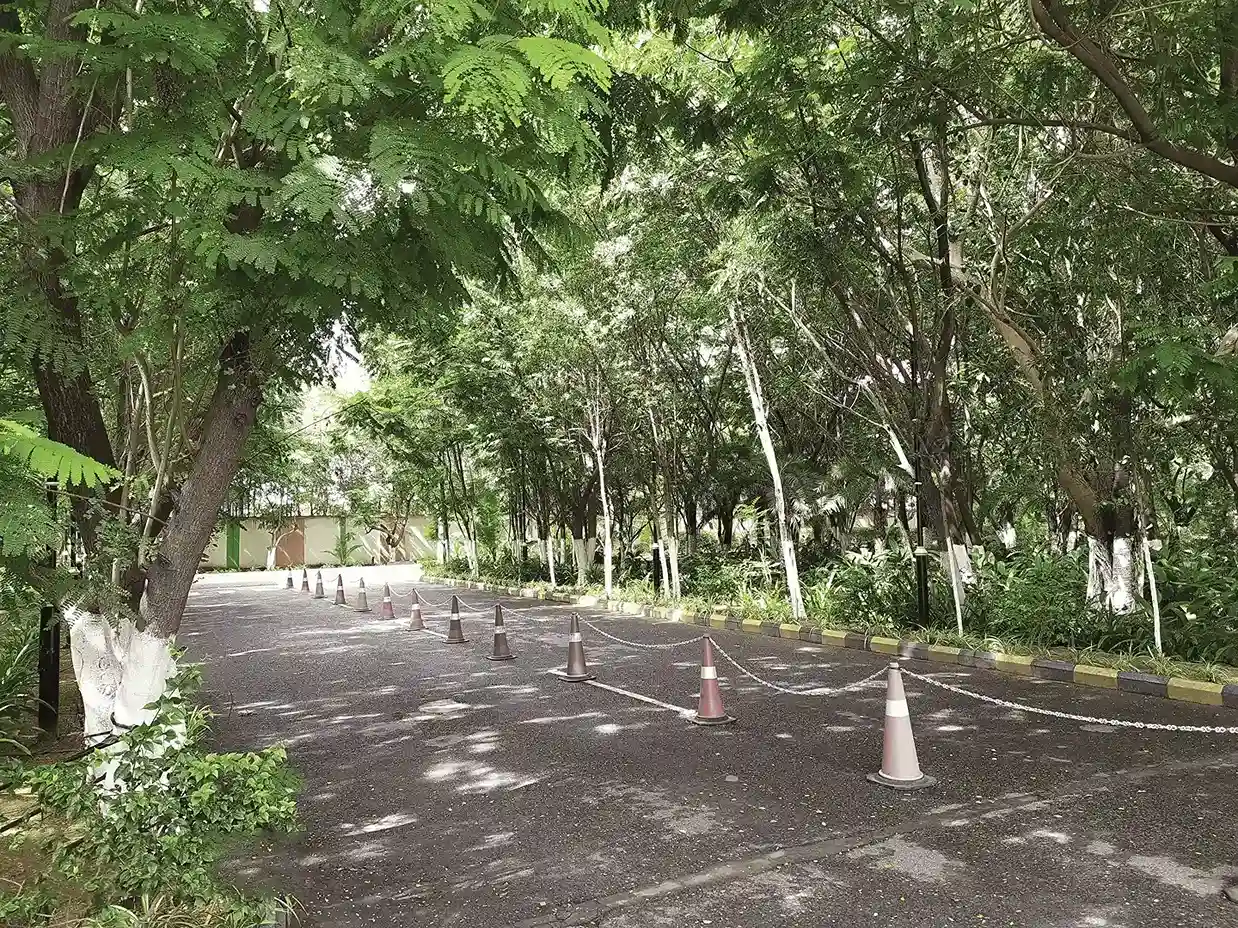
Case study
It’s not power plant operations,
but the soil affects the yield!
Perception:
The soil around our plant is sandy due to its proximity to the sea, being only 500 meters away. It is generally believed that the sandy soil is unsuitable for paddy cultivation because it cannot retain water throughout the day, which is crucial for paddy growth. Additionally, there is a public perception that the operations of the thermal power plant negatively affect crop yields. However, we strongly believe that the power plant’s operations do not impact the yield of paddy or other crops. To demonstrate this, our Greenbelt team has conducted an experiment within our plant premises to challenge these perceptions, and the results are very encouraging.
Experiment:
Our team has selected a new ‘Trail Crop on Plastic Sheet’ model to undertake an experiment to grow paddy in an
area of 1,000 square meters inside our Project – 2 (P-2).
Nellore Jilakara, a popular local variety of paddy, has been selected for this experiment.

Dug the soil up to 1.5 feet of depth
Area: 25 Meters of length and 4 Meters of width
The plastic sheet was layered and filled with better soil up to 1 foot level

100kgs of dry leaf manure and 150kgs of FYM were applied.
Provided the irrigation with the help of a water tanker.

Examined for water leaks for three days and found none.
Transplanted the paddy seedlings and continued the watering with a tanker once every five days.

Applied fertiliser for nutrition balance, such as 5 kg of vermicompost.
Drying

Status

Yeild - 1500 kgs

Result:
Farmers in the community get a yield of about 80 bags (50 kg) per acre, i.e., 0.98 kg per sq m.
Our new model has achieved a yield of 3 bags (50 kg) per 100 sq m, i.e., 1.5 kg per sq m which is almost 50% higher yield compared to the conventional farming in this region.
The better yield was possible because of:
Mulch system due to which there is
Less weeding
Less manpower
High disease resistance
100% fertiliser utilisation (Zero wastage)
Conclusion:
After the preliminary experiment, we conducted another trial over the course of one year in the same area and
location using the same model. The crop yield was moderately similar in both tests, confirming the validity of
the experiment. This demonstrates that the operations of the power plant are not affecting the yield, but the
soil is.
Appreciation
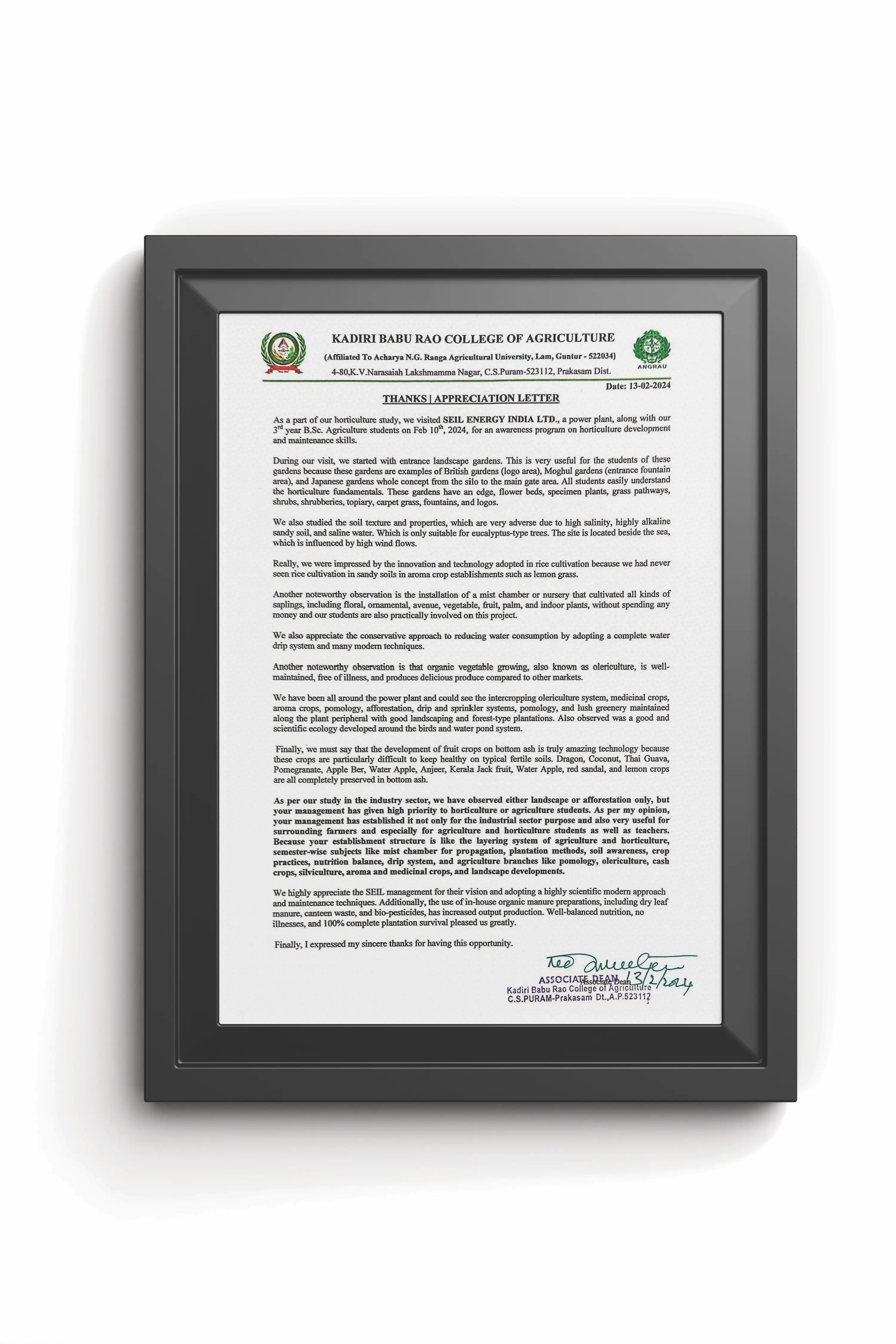